The company performs specialized examinations of vehicles, such as passenger cars, trucks, buses, semi-trailers, trailers, agricultural tractors, excavators, among others, using specialized diagnostic equipment. My Bureau uses the latest techniques to reconstruct accidents using relevant data contained in vehicle electronics. The bureau independently reads data from vehicle electronics. The bureau verifies this data by expertly examining the vehicle’s data readings, as well as based on data from another source. For such determinations, it uses, among others, the PicoScope 4425A oscilloscope, whose software makes it possible to determine the correctness of the communication signal and a number of specialized tests, including the testing of hybrid, electric cars. When performing diagnostics, reading data-especially from a vehicle that has been damaged-the basic issue is to determine whether the data provided are reliable or give errors due to damage. This is a basic element of the diagnostic procedure especially in the case of a car that has been damaged in an accident, collision. An example of EDR source data examination is shown below.
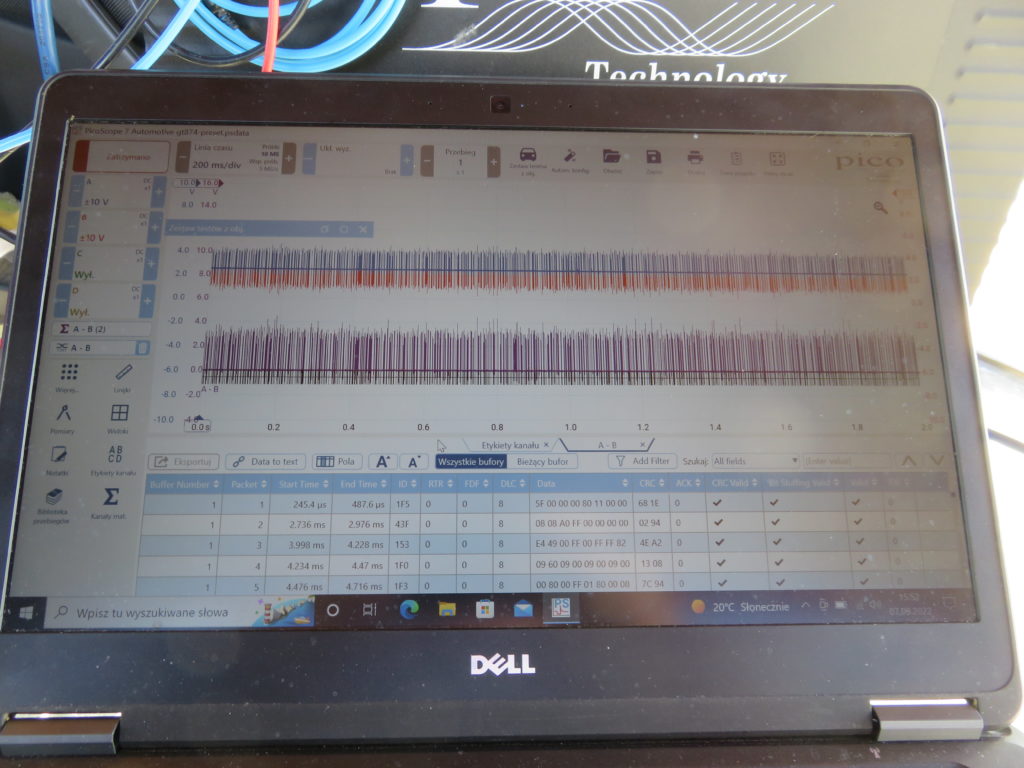
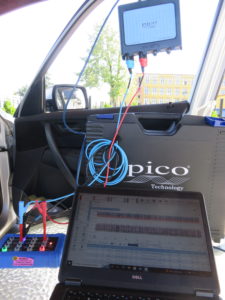
The test example shown above is an elementary way to check the reliability of the EDR data read. The manufacturer of the program provides the data (hexadecimal) on the basis of which the information given in the proto-collection was obtained. The operator specialist in EDR data interpretation is obliged to verify the obtained data (hexadecimal) from the controller, and therefore must perform a specialized examination of the EDR source data given at the end of the protocol.
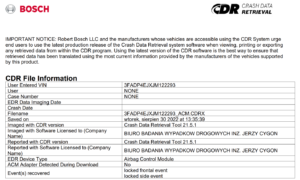
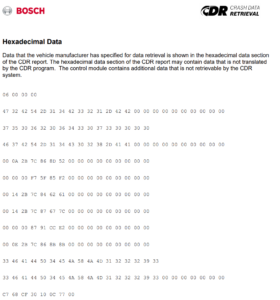
Testing the reliability of the EDR data is very important, and this is because the EDR data in most cases is stored in the airbag controller. The manufacturer of the airbag controllers does not allow repair of the airbag controllers, replacement with new ones is required. In contrast, in Poland, the repair of controllers is even common. When reading EDR data from the airbag controller, it is necessary first to determine whether this driver has not been repaired. If the airbag controller has been repaired, it is necessary to determine whether it was repaired correctly, as the above examination allows.
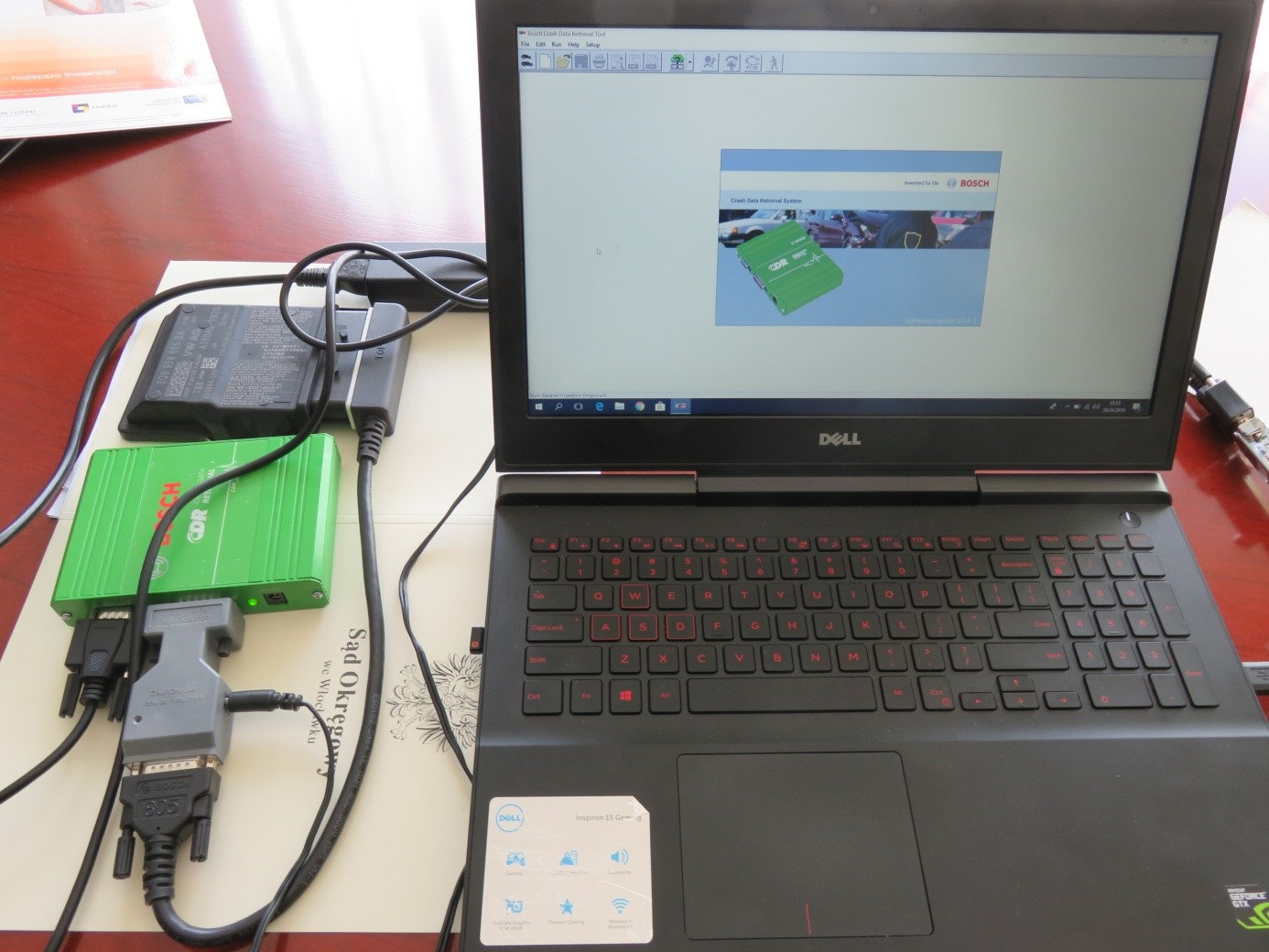
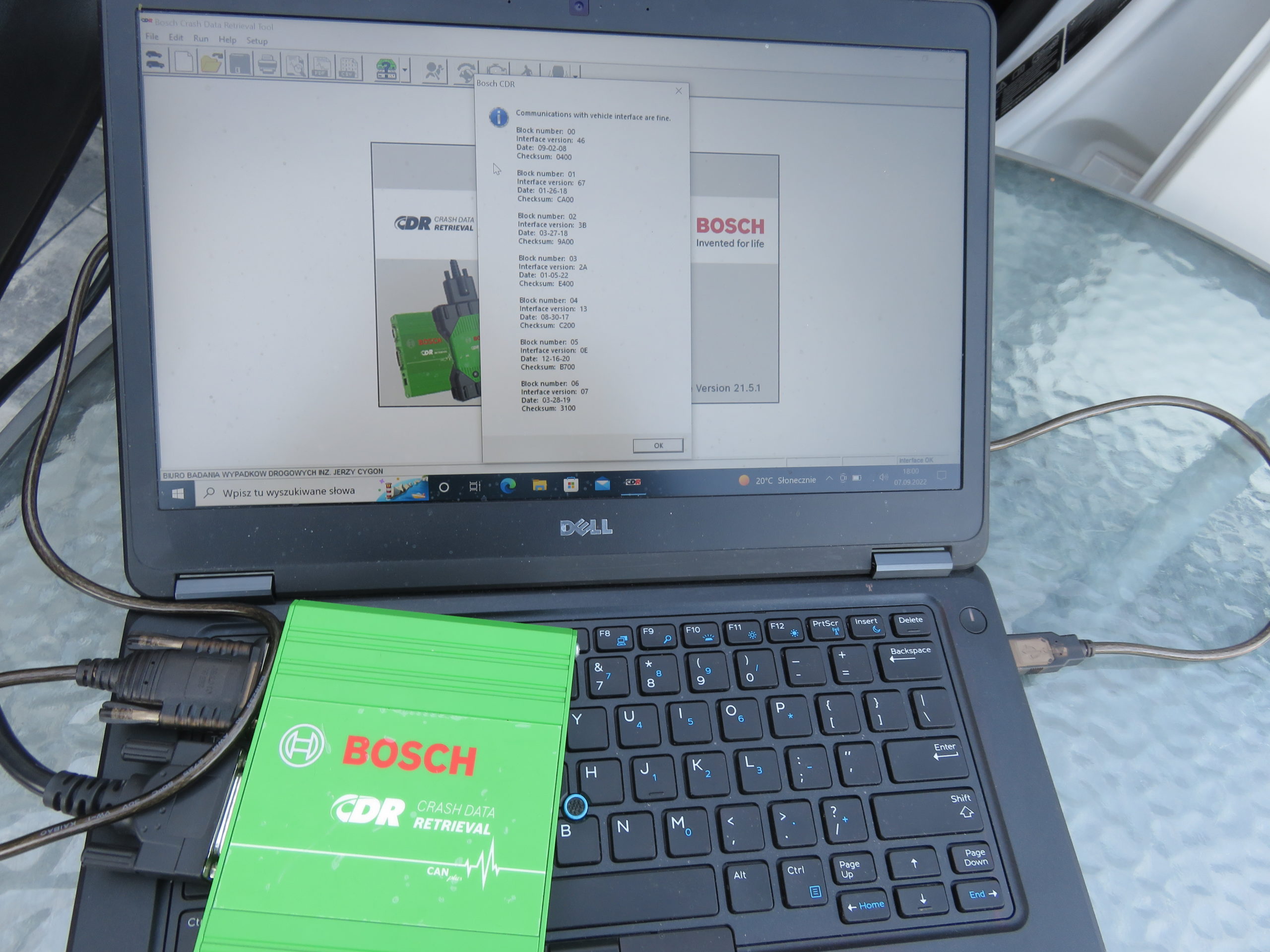
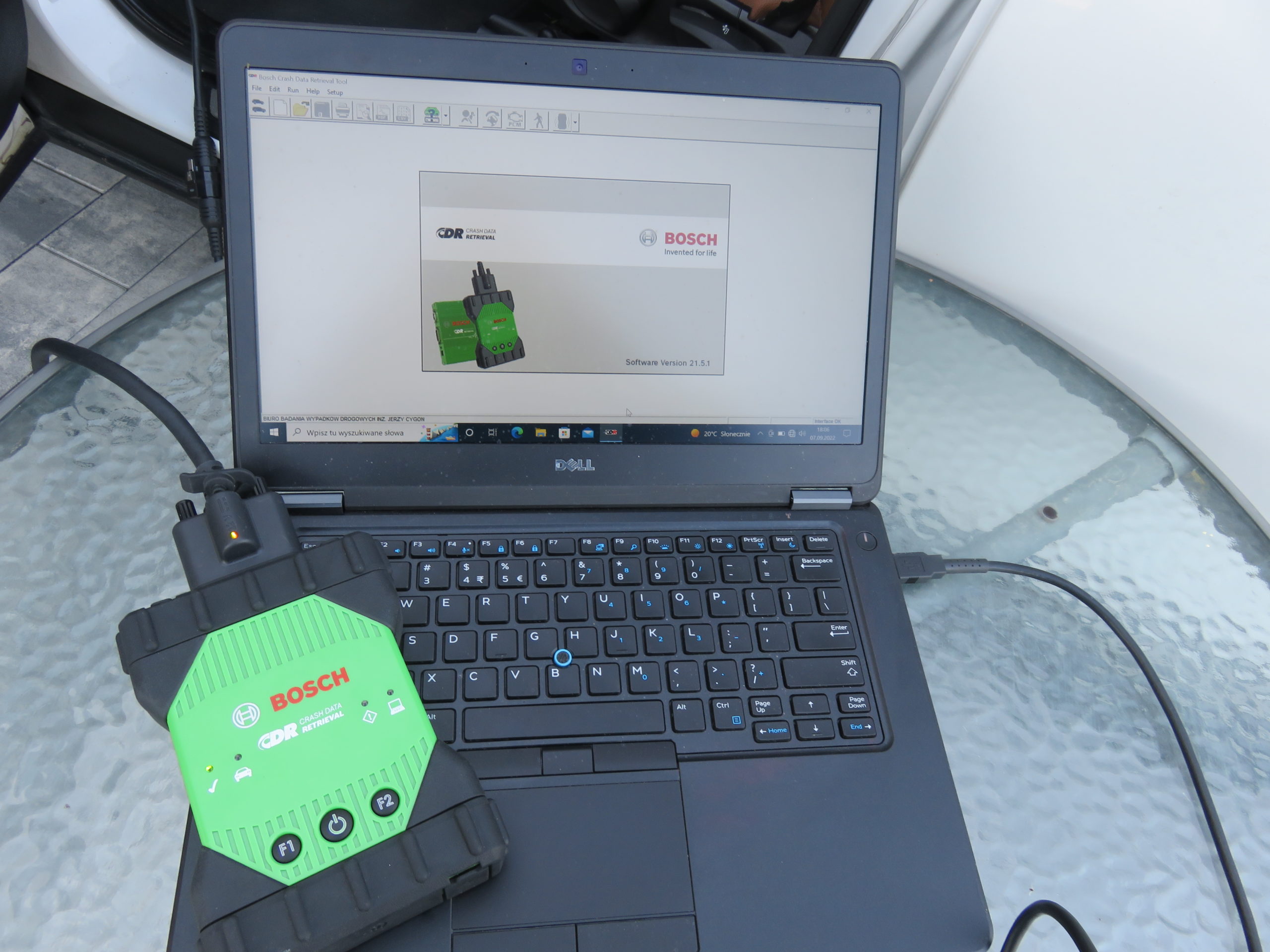
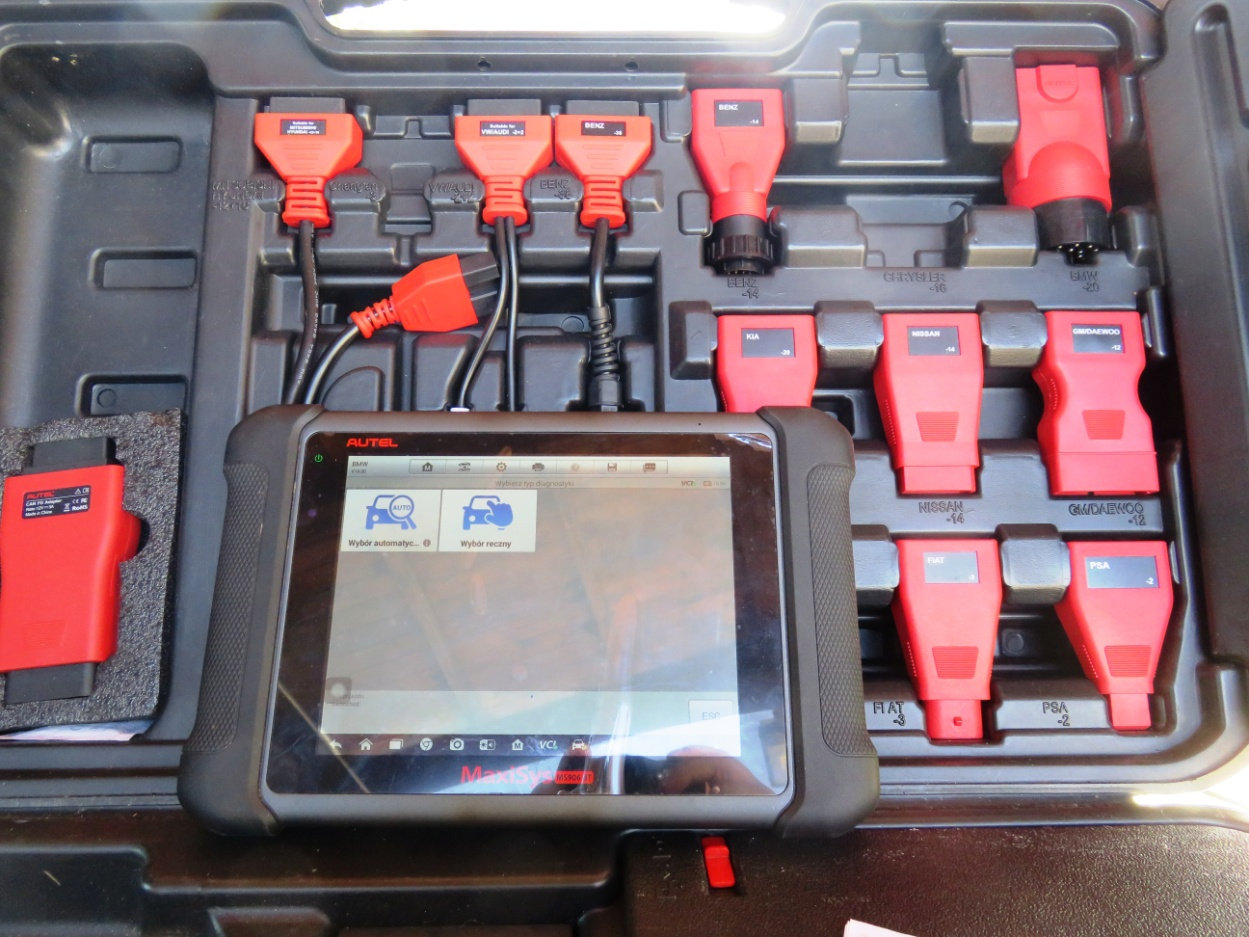

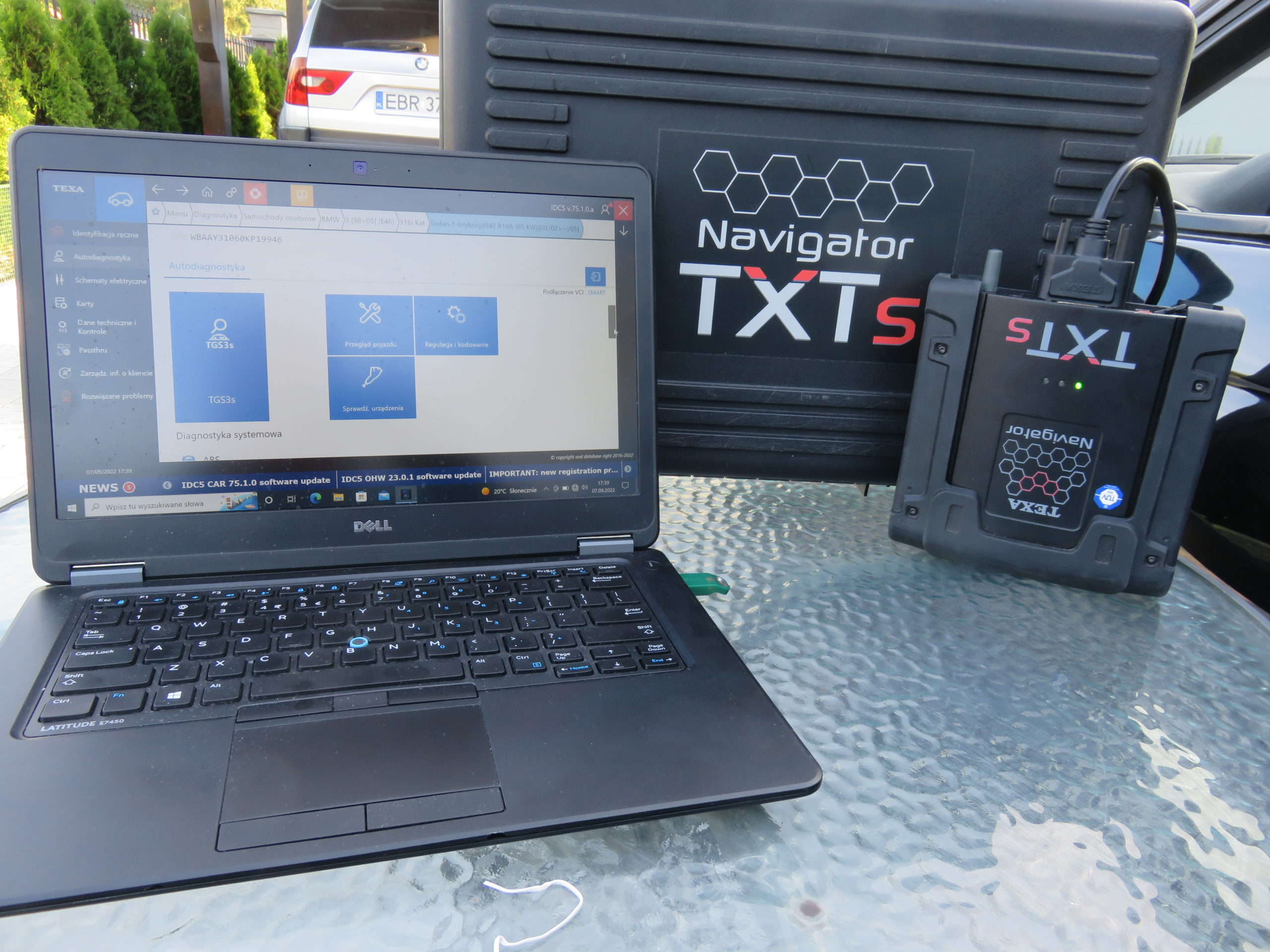

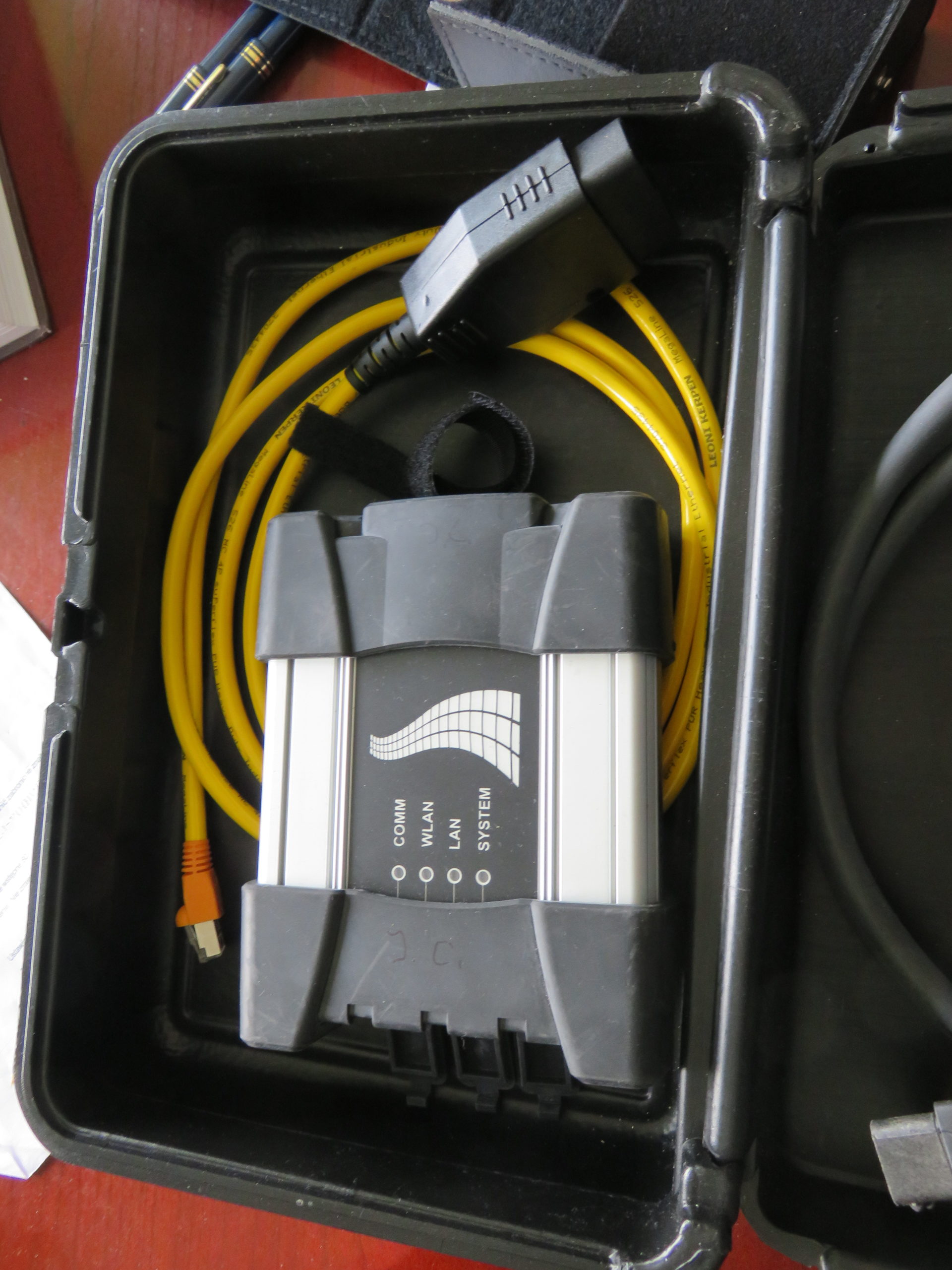
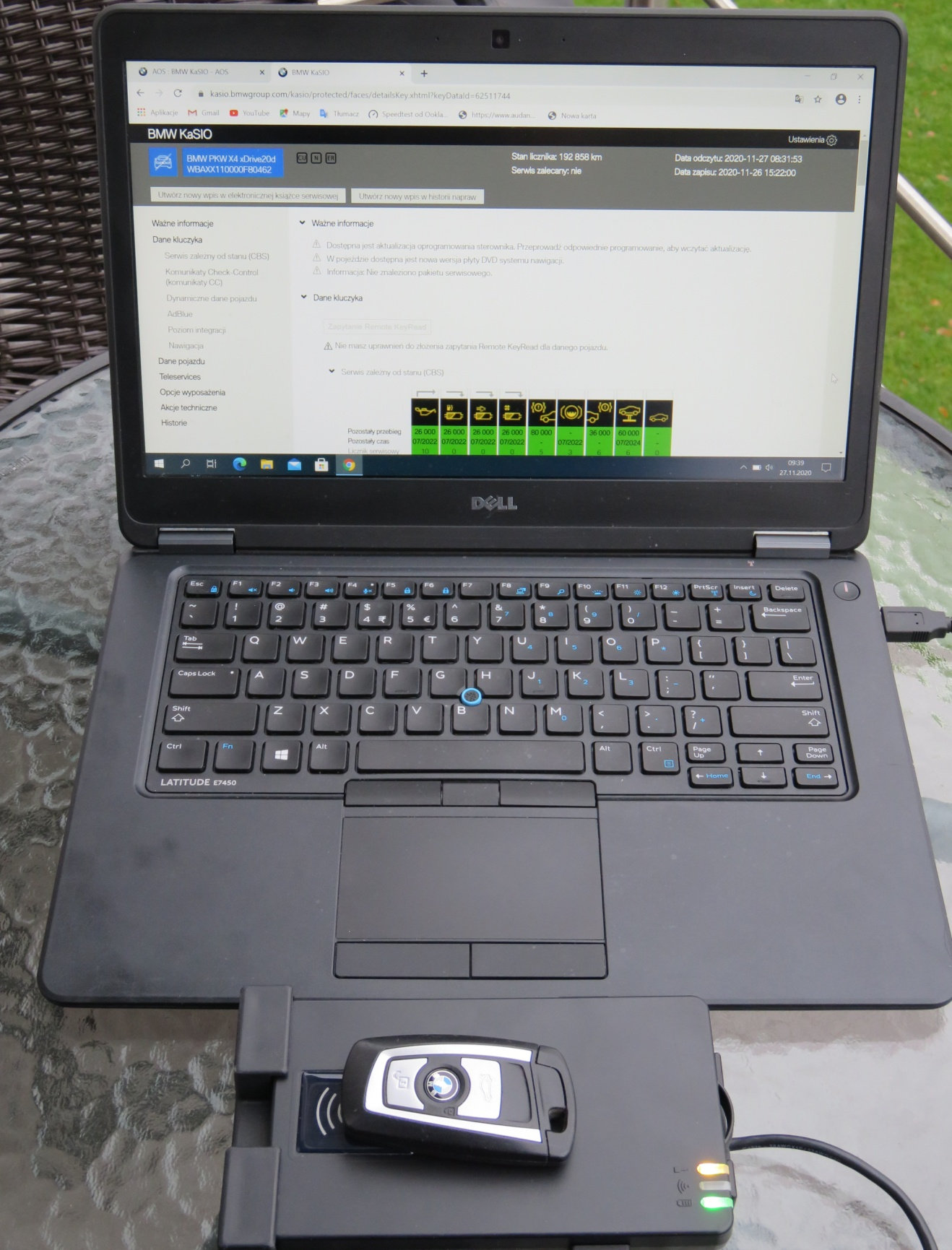
In the case shown below, the reading of CAN-data from freeze frames of error codes was sufficient information as to the speed of the car at the time of the first crash.
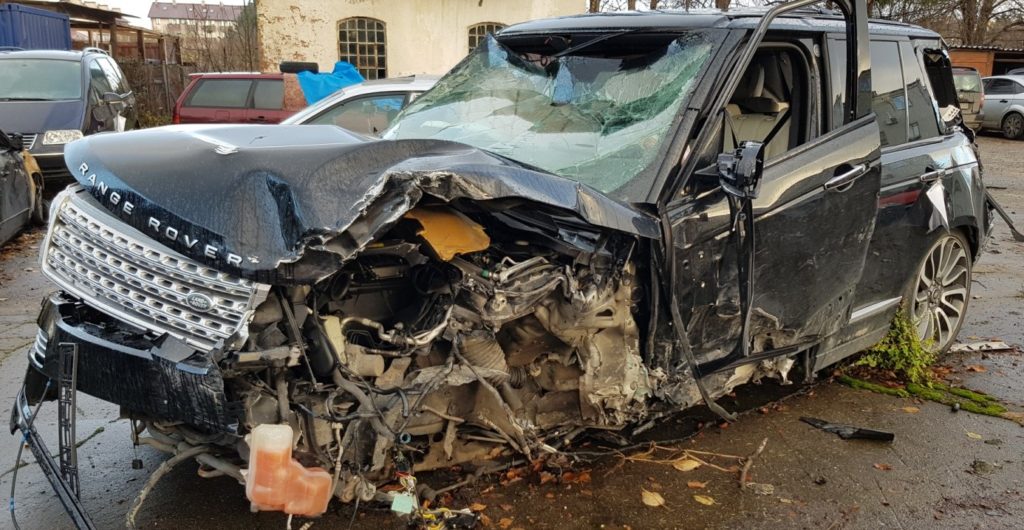
Engine RPM value | 3912 rpm |
Vehicle speed sensor | 134 km/h |
Time since engine start | 137 sec |
Reading data from the CAN allowed to unambiguously determine the actual course of the incident.
Reading data from CAN on, among other things, the braking process performed by the Volkswagen Passat ALLTRACK passenger car allowed the correct determination of the position of the car at the time of the first collision and the different conclusions of the opinion.
Below are some of the data (Volkswagen PASSAT):
Velocity_vehicle_reference: | 3.26 m/s |
Longitudinal_acceleration_vehicle_reference: | -1.58 m/s˛ |
Velocity_vehicle_reference: | 6.73 m/s |
Longitudinal_acceleration_vehicle_reference: | -9.51 m/s˛ |
Velocity_vehicle_reference: | 4.07 m/s |
Longitudinal_acceleration_vehicle_reference: | -11.66 m/s˛ |
Velocity_vehicle_reference: | 8.18 m/s |
Longitudinal_acceleration_vehicle_reference: | 0.57 m/s˛ |
Velocity_vehicle_reference: | 3.30 m/s |
Longitudinal_acceleration_vehicle_reference: | -1.49 m/s˛ |
Velocity_vehicle_reference: | 0.00 m/s |
Longitudinal_acceleration_vehicle_reference: | 0.00 m/s˛ |
Velocity_vehicle_reference: | 3.39 m/s |
Longitudinal_acceleration_vehicle_reference: | -5.16 m/s˛ |
Professional reading of data from the car’s electronics EDR, CAN, CAN FD allows you to determine whether the event took place as stated by the participants of the incident.
In the case of trucks, buses, trailers, semi-trailers, the relevant movement data is stored in the ODR, ECU and data stored in the CAN system freeze frames. I also read data from controllers that have been mechanically damaged.
For post-accident examination of braking systems of trailers, semi-trailers, trucks, autobu-s, I use a specialized device , which allows me, with the help of professional opro-gramming and specialized interfaces, to read data from the electronics of ODR, ECU, determine the actual state, including lighting – both at the time of the accident, as well as before the accident.
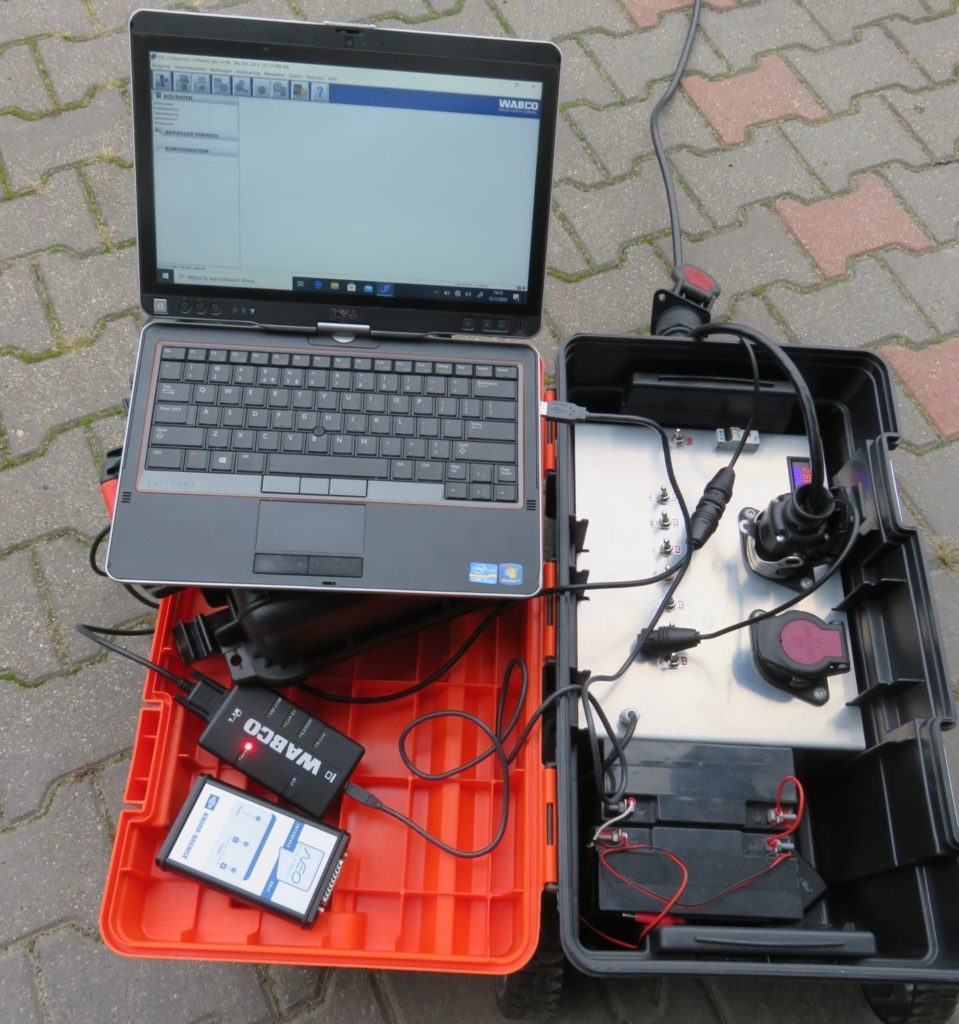
Below is part of the ODR data from the WABCO system. Due to the excessive amount of data I am not giving a full report.
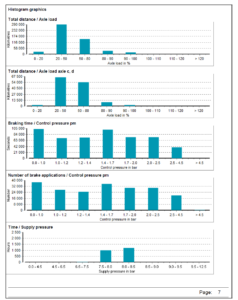
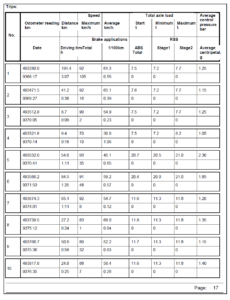
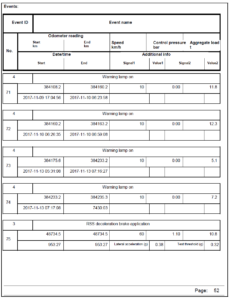
Digital tachograph data
In this case, the tire dimension data during validation is stored in the tachograph data storage. Reliability of the digital tachograph recording – the speed value reported is not always the actual speed value, and a number of analyses must be performed to check this, but the primary one is the reading from the ECU data controller, as the reliability of the data sent to the digital tachograph is of essence. Another issue is the fact that it is a recording to a time buffer and not on the fly. Therefore, such an important matter should be dealt with by people who have the required knowledge, equipment, software necessary for this type of analysis, and not only the authorization. Below is an example of a situation that the reported value of speed at the time of the collision we can not consider reliable, especially if the speed graph looks like the following:
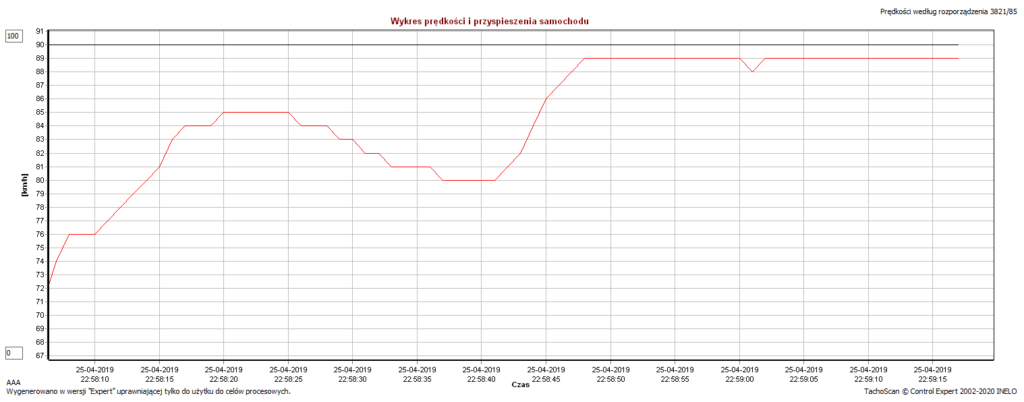
In this case, the important information that the reported speed immediately before the crash and especially at the time of the crash is unreliable was due to the configuration of the crash site and the video, which illustrates how the team moved relative to the double continuous line on such a complex road configuration.
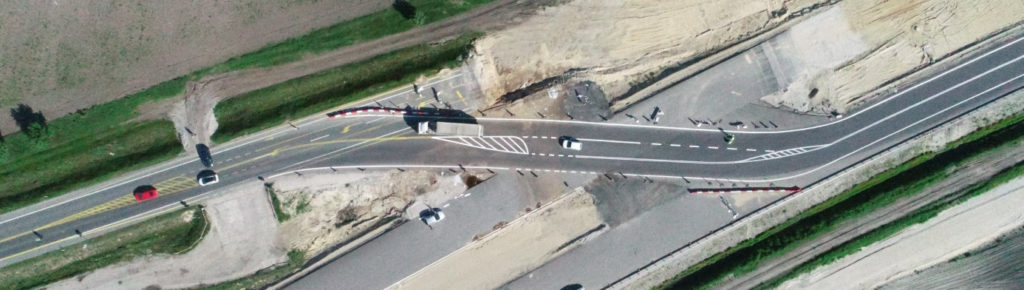
The driver of a Scania R440 tractor-trailer with a Krone brand semitrailer was moving as the tractor-trailer visible in the photograph. An analysis of the video in the case file shows that both the movement of the Scania R440 brand tractor and the Krone brand semi-trailer before the collision is stable, with no lateral drift, tilt, abandonment, etc.
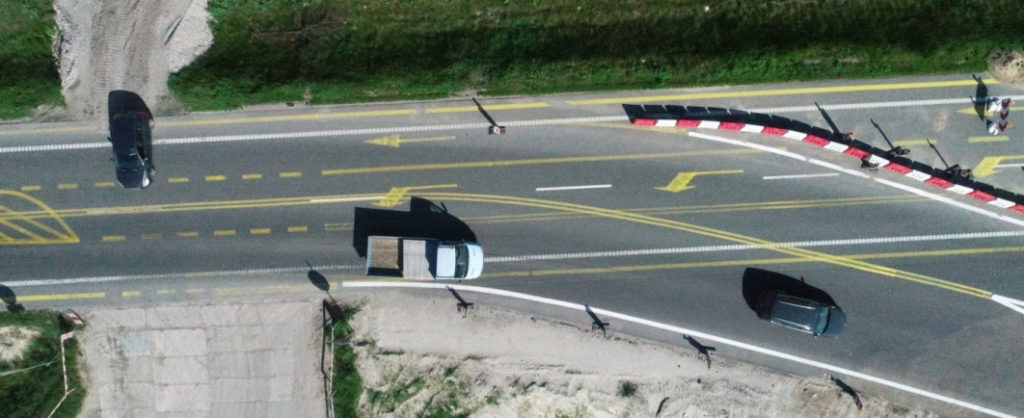
During the departure of a Scania R440 truck tractor with a Krone semi-trailer from the ”chic-ny”, there was a collision with a Volvo FH12 truck tractor with a LAG tank trailer, and practically it was mainly the semi-trailer.
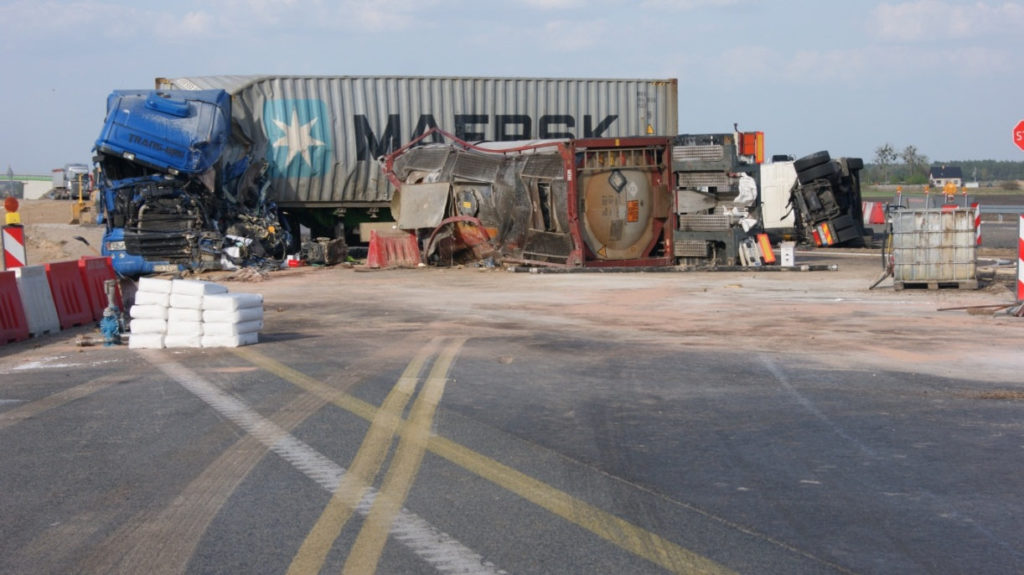
This material is important, because from the experience of carrying out this type of dynamic simulations, it is clear that with this spatial configuration of the road, such a type of motion of a Scania R440 truck tractor with a Krone semi-trailer, due to its dynamics, is technically impossible for the speed assumed in the case file (tachograph record) on this section of the road. This can be proven by conducting a dynamic simulation of the above incident using the PC Crash simulation program version 14.0. In this case, the configuration of the road and the evidence allowed clear conclusions that the accepted speed values from the digital tachograph record both at the time of the incident and immediately before the crash for the Scania R440 truck tractor with a Krone semi-trailer are false and contradict the elementary laws of physics. An elementary requirement of this type of record as well as all such data is to verify its reliability.
I made a reading from the controller responsible for the transmission and correctness of the pulse of the digital tachograph work. The report from the test below. From the test – data from the ECU, it appears that there was a failure of the system responsible for the correct operation of the digital tachograph.
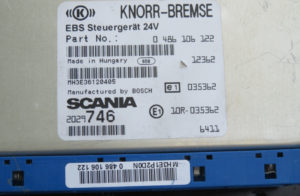
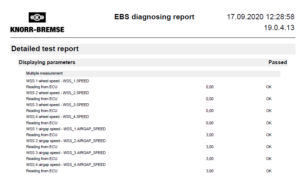